-
High-purity sintered porous 316L stainless steel steam filters effective retention of p...
SINTERED METAL FILTERS FOR THE REMOVAL OF PARTICLES High-purity filters and spargers are specially designed to meet strict requirements for the removal of pa...
View Detail -
High flow non-invasive ventilator Inspiratory Bacteria Filter air inlet medical grade ...
HENGKO's filter element of the ventilator is stainless steel 316, stainless steel 316L, which has the characteristics of filtering and dustproof. Its materia...
View Detail -
OEM high purity porous metal 316L chamber diffusers and filters
HENGKO OEM Gas Chamber Diffusers provide uniform and laminar gas flows without disturbing particles in the chamber. These diffusers also remove particles fro...
View Detail -
Porous Metal Filter For Culture Vessel OEM and Custom
High-purity filters and spargers are specially designed to meet strict requirements for the removal of particles in process gases in, for example, semiconduc...
View Detail -
Inspiratory bacteria/viral respiratory Filter with heat and moisture exchange 316 316L...
HENGKO's filter element of the ventilator is stainless steel 316, stainless steel 316L, which has the characteristics of filtering and dustproof. Its materia...
View Detail -
HENGKO Inspiratory Bacteria non invasive assisted mini personal lung Ventilation medic...
HENGKO's filter element of the ventilator is stainless steel 316, stainless steel 316L, which has the characteristics of filtering and dustproof. Its materia...
View Detail -
Porous filters liquid-solid process filters for high temperature & corrosive envir...
HENGKO offers liquid-solid process sintered metal filters for high-temperature & corrosive environments. HENGKO manufactures filter elements in a ...
View Detail -
High-temperature adaptable exhaust flue gas sampling probe filter element for industria...
HENGKO stainless steel probe is one of the most popular gas probes.It comes with a water/dust stop filter mounted to the tip to protect the probe, sample lin...
View Detail -
Custom sintered stainless steel round disc filter for flameproof and fire resistance
Sintered metal materials are a popular choice because these highly engineered materials consist of a uniform, interconnected porosity that can be fabricated ...
View Detail -
Household non-invasive High-Acuity ventilator expiratory flow diaphragm oxygen gas chok...
HENGKO's sintered bacterial viral filters of the ventilator are stainless steel 316, and stainless steel 316L, which have the characteristics of filtering an...
View Detail -
OEM sintered stainless steel porous metal fluidizers fluid for material transfer or tra...
HENGKO’s porous metal fluidizers provide an optimum solution for material transfer or transport applications that require strength, elevated temperature tole...
View Detail -
Sintered Metal Fame Arrestors Manufacturer for the Storage and Transportation of Inflam...
Flame Arrestors are safety devices that allow the flow of combustible gases while preventing ignition. The Flame Arrestorprevents the flame from transferring...
View Detail -
Household non-invasive Ventilator anesthesia machine 316 316L stainless steel with adj...
HENGKO's filter element of the ventilator is stainless steel 316, stainless steel 316L, which has the characteristics of filtering and dustproof. Its materia...
View Detail -
Tidal Volume Delivery From Medical ICU Respiratory Mechanical Ventilation Filter , 316...
HENGKO's filter element of the ventilator is stainless steel 316, stainless steel 316L, which has the characteristics of filtering and dustproof. Its materia...
View Detail -
Porous metal flow restrictors used in require anti-clogging or laminar flow applications
HENGKO delivers precision porous metal flow restrictors that provide a reliable and economical replacement for small control valves. A porous metal flow rest...
View Detail -
High Purity Flow Restrictors uesd in high-flow C-Seal configuration gas systems / flow ...
HENGKO delivers precision porous metal flow restrictors that provide a reliable and economical replacement for small control valves. A porous metal flow rest...
View Detail -
Medical Bacterial/Viral tidal volume delivered filter with heat and moisture exchange ...
HENGKO's filter element of the ventilator is stainless steel 316, stainless steel 316L, which has the characteristics of filtering and dustproof. Its materia...
View Detail -
Gas Diffusion Layers Sheet for MEAs, stainless steel porous metal sintered / wire mesh ...
HENGKO stainless steel filter plates are made by sintering 316L powder material or multilayer stainless steel wire mesh at high temperatures. They have been ...
View Detail -
HENGKO medical Respiratory Mechanical tidal volume delivered filter for ventilator brea...
HENGKO's filter element of the ventilator is stainless steel 316, stainless steel 316L, which has the characteristics of filtering and dustproof. Its materia...
View Detail -
High flow non-invasive ventilator circuit bacteria air inlet medical grade 316L stainl...
HENGKO's filter element of the ventilator is stainless steel 316, stainless steel 316L, which has the characteristics of filtering and dustproof. Its materia...
View Detail
Types of Sintered Filter Elements
Sintered filter elements are porous metal components formed by heating metal powder or fibers without melting them, causing them to bond together. They offer a unique combination of high strength, permeability, and precise filtration capabilities, making them ideal for various industrial applications.
Here are the main types of sintered filter elements:
1. Sintered Metal Mesh Filter Discs/Plates:
These are the most common type, made by layering and sintering multiple layers of fine metal mesh.
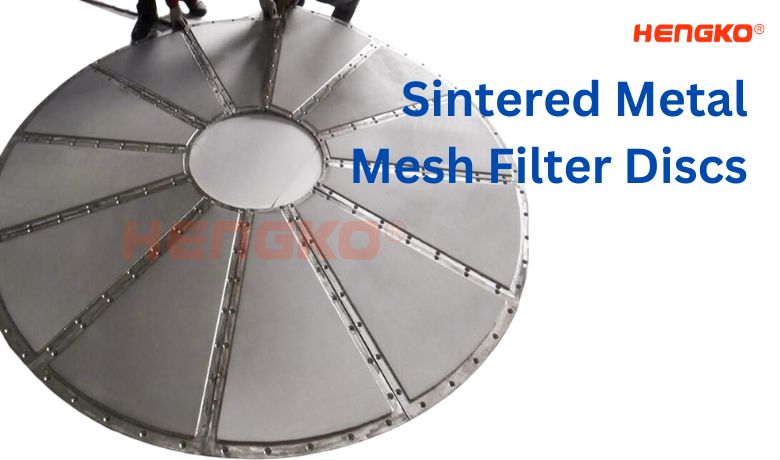
* They offer high flow rates, good dirt-holding capacity, and are easily backwashed for cleaning.
* Commonly used in liquid and gas filtration applications.
2. Sintered Metal Fiber Felt Filter Cartridges:
* These are made from randomly oriented metal fibers sintered together to form a felt-like structure.
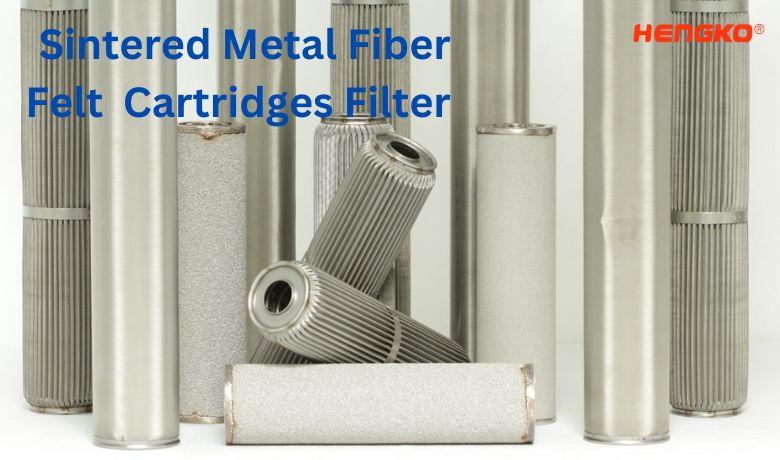
Sintered Metal Fiber Felt Filter Cartridges
* They offer excellent depth filtration, capturing particles throughout the cartridge thickness.
* Suitable for high-temperature and high-pressure applications, as well as for filtering viscous fluids.
3. Sintered Metal Powder Filter Elements:
These filter are formed by sintering metal powder into a specific shape, often with controlled porosity and pore size distribution.
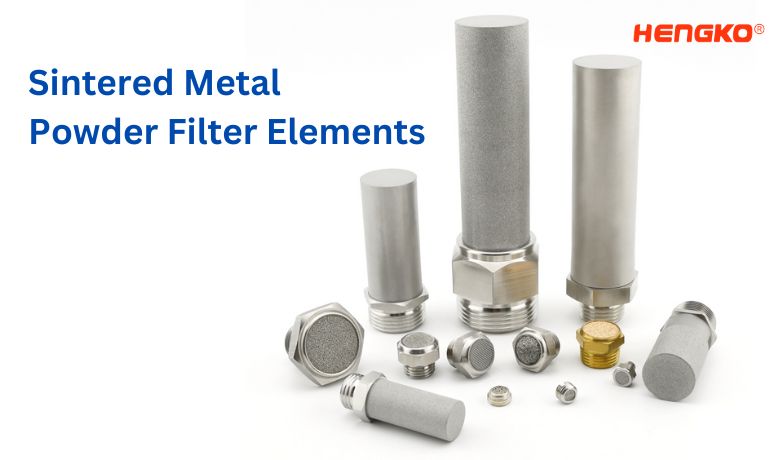
Sintered Metal Powder Filter Elements
They offer precise filtration down to very small particle sizes and are often used in critical applications like aerospace and medical devices.
4. Combination Filter Elements:
* These combine different types of sintered media, such as mesh and powder, to achieve specific filtration characteristics.
* For example, a mesh-on-powder element might offer both high flow rate and fine filtration.
The choice of sintered filter element type depends on several factors, including the desired filtration efficiency, flow rate,
pressure drop, operating temperature, and fluid compatibility.
Here are some additional materials used in sintered filter elements:
* Stainless steel: The most common material, offering good corrosion resistance and strength.
* Bronze: Good for acidic and high-temperature environments.
* Nickel: Offers excellent corrosion resistance and high strength.
* Titanium: Lightweight and highly corrosion-resistant, suitable for demanding applications.
Why Custom HENGKO Sintered Filter Element
and Instrument Components
As One of leading factory for sintered metal filter, HENGKO supply customize any innovative
design for various applications.
We offer best solutions to fulfill requirements for petrochemical, fine chemical, water treatment,
pulp and paper, auto industry, food and beverage, metalworking, etc.
✔ Over 20 years of experience as a professional sintered stainless steel filter manufacturer in the powder metallurgy industry
✔ Strict CE and SGS certification for our 316 L and 316 stainless steel powder filters
✔ Professional high temperature sintered machines and die casting machines
✔ A team of 5 engineers and workers with over 10 years of experience in the stainless steel filter industry
✔ Stainless steel powder materials stock to ensure fast manufacturing and shipping.
As One of Best Filter Element Manufacturer, HENGKO Focus on Quality and on Time Delivery Over 15 Years. Find HENGKO and Try
Samples, Know the difference and Top Quality Sintered Metal Filters.
Types of Sintered Metal Filter Elements by Materials
Here are some types of high-demanding sintered metal filter elements:
1. Stainless Steel Sintered Filters:
2. Bronze Sintered Filters:
3. Titanium Sintered Filters:
4. Nickel Sintered Filters:
5. Inconel Sintered Filters:
6. Hastelloy Sintered Filters:
7. Monel Sintered Filters:
8. Copper Sintered Filters:
9. Tungsten Sintered Filters:
10. Porous Stainless Steel Filters:
11. Sintered Mesh Filters:
12. Powder Metal Filters:
13. Sintered Metal Fiber Filters:
These high-demanding sintered metal filter elements are used in diverse industries, including petrochemicals, aerospace, pharmaceuticals, automotive, food processing, and many others, where efficient and reliable filtration is crucial to the processes and product quality.
Main Applications Demanding Sintered Filter Element
Petrochemical, Fine Chemical, Water Treatment, Pulp and paper, Automobile Industry,
Food and Beverage, Metal Processing and other Industries
1. Liquid Filtration
2. Gas Filtration
3. Fluidizing
3. Sparging
4. Diffusion
5. Flame Arrestor
Engineered Solution Support
In the past 20 years, HENGKO has solved over 20,000 complex filtration Instrument & Components and flow
control problems for customers worldwide in a wide range of industries. Solving complex engineering tailored
to your application, We believe we can find the best solution for your filters requirement soon.
Welcome to Share Your Project and Require Details.
We will supply Best Professional Solution of Instrument & Components For Your Projects soon.
You are welcome to Send Inquiry by Following Form and let us know details about your requirement
for the Sintered Filter Element and Instrument Components
Also you can send email directly to Mrs. Wang by ka@hengko.com
FAQs
1. What are sintered filter elements, and how do they work?
Sintered filter elements are a type of filter made by fusing (or "sintering") together small particles, typically of metal or ceramic, to form a porous structure. These filters are used in various applications where precise filtration, high strength, and good corrosion resistance are required. Here's a more detailed explanation:
How Sintered Filter Elements are Made:
1. Raw Material Selection: The process begins with the selection of raw materials, usually metal powders like stainless steel, bronze, or titanium, or ceramic powders.
2. Forming: The selected powder is then formed into the desired shape, often using a mold. This can be done through pressing or other shaping methods.
3. Sintering: The shaped material is then heated in a controlled environment (often in a furnace) to a temperature below its melting point but high enough to cause the particles to bond together. This process results in a solid structure with interconnected pores.
How They Work:
1. Porous Structure: The sintering process creates a porous structure, where the size of the pores can be controlled by adjusting the sintering conditions and the size of the starting particles. This allows for precise control over the filtration properties.
2. Filtration Mechanism: When a fluid (either liquid or gas) is passed through the sintered filter, particles larger than the pore size are trapped on the surface or within the pores of the filter, while smaller particles and the fluid itself pass through. This effectively separates the undesired particles from the fluid.
3. Backwashing: One of the advantages of sintered filter elements is that they can often be cleaned and reused. In many applications, this is done by backwashing, where the flow of fluid is reversed to dislodge trapped particles.
Advantages of Sintered Filter Elements:
1. High Strength: Due to the sintering process, these filters have high mechanical strength, making them suitable for applications with high pressures or where mechanical stresses are a concern.
2. Thermal Stability: They can operate at higher temperatures than many other types of filters.
3. Corrosion Resistance: Depending on the material used, sintered filters can be highly resistant to corrosion, making them suitable for aggressive environments.
4. Precise Filtration: The pore size can be precisely controlled, allowing for accurate filtration down to very small particle sizes.
5. Long Service Life: They can be cleaned and reused multiple times, leading to a longer service life compared to some other filter types.
Sintered filter elements are used in a wide range of applications, including chemical processing, food and beverage production,
pharmaceutical manufacturing, and gas purification, among others.
2. What are some common applications for sintered filter elements?
Sintered filter elements, known for their durability and ability to filter at high temperatures and pressures,
have a wide range of applications across various industries. Here are some common ones:
*Chemical Processing:
Sintered filters are used in chemical plants for filtering corrosive liquids and gases.
Their resistance to corrosion and high temperatures makes them ideal for this demanding environment
*Petroleum Refining:
In refineries, these filters help separate contaminants from fuels during the refining process.
Their ability to handle high temperatures and not react with the fuel makes them valuable
*Food and Beverage:
Sintered filters ensure purity and clarity in beverages and edible oils by removing unwanted particles during processing
*Pharmaceuticals:
Maintaining sterility is crucial in pharmaceutical production. Sintered filters are used to sterilize fluids and remove
contaminants in this industry
*Water Treatment:
These filters play a role in water treatment facilities by removing impurities and suspended solids from water
*Domestic Appliances:
Sintered filter elements are found in common household appliances like vacuum cleaners and water purifiers,
helping maintain cleanliness and performance
*Electronics Industry:
They are used to ensure clean air circulation around sensitive electronic components, protecting them from contaminants
*Nuclear and Energy Industry:
Their ability to handle high pressure and resistance to corrosion makes them suitable for filtering coolants in nuclear reactors
and other high-pressure applications in the energy sector.
This is not an exhaustive list, but it highlights the versatility of sintered filter elements in various applications
where efficient filtration and durability are essential.
3. What are the advantages of using sintered filter elements?
Using sintered filter elements offers several advantages in various industrial applications. Here are some of the key benefits:
1. High Filtration Efficiency:
Sintered filters provide excellent filtration efficiency due to their controlled pore structure. They can effectively remove particles of various sizes, ensuring cleaner and purer fluids or gases.
2. Durability and Longevity:
Sintered filter elements are made from robust materials like stainless steel, bronze, or ceramics, which make them highly durable and resistant to wear and tear. They have a longer service life compared to other types of filters.
3. Temperature and Chemical Resistance:
Sintered filters can withstand a wide range of temperatures and are chemically resistant, making them suitable for use with aggressive fluids and in harsh environments.
4. Corrosion Resistance:
Sintered filters made from materials like stainless steel and certain alloys exhibit exceptional corrosion resistance, making them ideal for applications involving corrosive fluids or gases.
5. High Flow Rates:
The porous structure of sintered filters allows for high flow rates while maintaining effective filtration. This is crucial in processes that require fast filtration without compromising on filtration quality.
6. Uniform Pore Size Distribution:
Sintering processes enable precise control over the pore size distribution, resulting in consistent and reliable filtration performance.
7. Low Pressure Drop:
Sintered filters offer low pressure drop across the filter media, reducing energy consumption and minimizing the strain on the system.
8. Easy to Clean and Maintain:
Sintered filters can be easily cleaned through backwashing, ultrasonic cleaning, or mechanical methods, allowing for extended use and reduced replacement frequency.
9. Wide Range of Applications:
Sintered filter elements find applications in various industries, including oil and gas, chemical processing, pharmaceuticals, food and beverage, water treatment, automotive, aerospace, and more.
10. Versatility:
Sintered filters can be designed and manufactured in various shapes and sizes, making them adaptable to different filtration systems and equipment.
11. Sterilization Capability:
Sintered filters made from certain materials, such as titanium or zirconia, can withstand high-temperature sterilization processes, making them suitable for critical applications in healthcare and biotechnology.
Overall, the advantages of using sintered filter elements make them a preferred choice in situations where efficient and reliable filtration is essential for process efficiency, product quality, and equipment protection.
4. How long do sintered filter elements last?
The lifespan of a sintered filter element depends on the specific application and operating conditions.
In general, sintered filter elements have a longer lifespan than other filters due to their strength and durability.
But also , You Know lifespan of sintered filter elements can vary depending on several factors, including the material of construction, operating conditions, the level of contaminants, and the maintenance practices. Generally, sintered filter elements are known for their durability and longevity compared to other types of filters. Here are some considerations that affect their lifespan:
1. Material of Construction:
The choice of material for the sintered filter element plays a significant role in its longevity. Filters made from durable materials like stainless steel, bronze, titanium, or ceramics tend to have longer lifespans compared to filters made from less robust materials.
2. Operating Conditions:
The conditions under which the filter operates can influence its lifespan. Extreme temperatures, aggressive chemicals, and high pressures can put additional stress on the filter, potentially affecting its longevity.
3. Level of Contaminants:
The amount and type of contaminants in the fluid or gas being filtered can impact the filter's lifespan. Filters dealing with higher levels of particulates or corrosive substances may need more frequent replacements.
4. Maintenance and Cleaning:
Proper maintenance and cleaning of the sintered filter elements can extend their lifespan. Regular cleaning and adherence to recommended maintenance schedules can help prevent clogging and maintain filtration efficiency.
In general, well-maintained sintered filter elements can last for several years before needing replacement. However, it's essential to monitor the filter's performance regularly and replace it when it starts to show signs of reduced efficiency or clogging. Manufacturers or suppliers often provide guidelines on the expected lifespan of their specific filter products, which can serve as a reference for replacement intervals.
5. Can sintered filter elements be cleaned and reused?
Some sintered filter elements can be cleaned and reused, depending on the type of filter media and the operating conditions. It is important to follow the manufacturer's cleaning and maintenance recommendations to ensure the filter element's longevity and performance.
6. What are OEM-demanding sintered filter elements?
OEM-demanding sintered filter elements are custom-made filter elements designed and manufactured to meet the specific needs of an Original Equipment Manufacturer (OEM). They are typically used in specialized equipment or systems where standard filter elements may not be suitable.
7. How do I determine my application's correct sintered filter element?
There are several factors to consider when selecting a sintered filter element, including the type of fluid or gas being filtered, the operating temperature and pressure, the desired filtration efficiency, and the size and shape of the filter element. It is important to consult with a filter element specialist or manufacturer to determine the best fit for your specific application.
8. Can sintered filter elements be customized to meet my specific needs?
Yes, you can customize sintered filter elements to meet the specific needs of an application. OEM-demanding sintered filter elements are a common example of customized filter elements.
9. What are the advantages of using OEM demanding sintered filter elements?
OEM-demanding sintered filter elements offer several advantages, including a perfect fit for the intended application, improved performance and efficiency, and the ability to meet unique requirements or specifications.
10. How long does it take to manufacture OEM-demanding sintered filter elements?
The manufacturing time for OEM demanding sintered filter elements will depend on the complexity of the design and the number of filters being produced. When placing an order, it is important to discuss lead time with the manufacturer or filter element specialist.
Contact HENGKO Today!
For all your inquiries and filtration needs, don't hesitate to reach out to us at HENGKO.
Email us at ka@hengko.com and our dedicated team will be delighted to assist you.
Experience top-quality filtration solutions with HENGKO - Contact us now!
Send your message to us: