OEM Special Sintered Cartridge Filter
HENGKO supplies customized solutions for sintered metal cartridge filter, including technical support throughout the process, from design and development to delivery.
① We offer a wide range of materials for option, including stainless steel, bronze, nickel, and other alloys
② Customize size, shape, and properties to meet the specific needs of their clients.
③ OEM pore size for your special filtration system requires
Because of high performance, durability, and resistance, High temperature resistant, and corrosion, our sintered metal cartridge filters have a wide range of applications,
including cup design filtration elements, aeration stone, sensor probe, and more.
So if you also looking for special filter or protector solution? Contact HENGKO, and we will supply some better ideas for your filtration solution soon.
* OEM Cartridge Metal Filter Materials
HENGKO is a manufacturing entity that has been specializing in Sintered Metal Filters for over 18 years. Up to date, we have been providing superior quality sintered cartridges made from materials such as 316L, 316, Bronze, Inco Nickel, Composite Materials, and more.
* OEM Sintered Cartridge Filter By Pore Size
To achieve superior filtration results, the initial step is selecting the appropriate pore size for your sintered cartridge, which should align with your specific filtration technical needs. Feel free to reach out to us for any queries related to choosing the correct pore size.
* OEM Sintered Cartridge Filter By Design
In terms of shape design and size, we offer three primary types: the open-bottom cylindrical, the cup-shaped design, and a variety of standard shapes. We also provide custom-shaped designs with optional connectors to meet unique requirements.
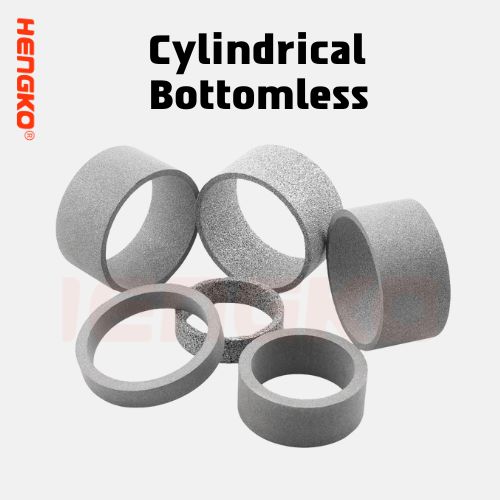
oem Bottomless Cylindrical sintered cartridge
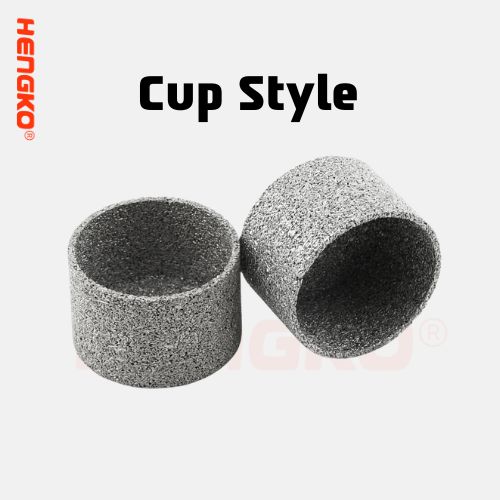
OEM cup design sintered metal cartridge
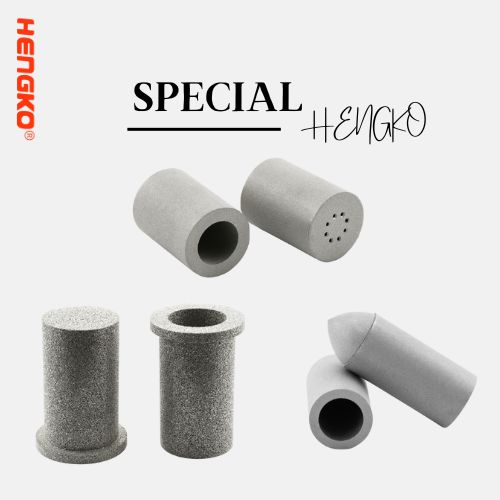
OEM special design sintered metal cartridge
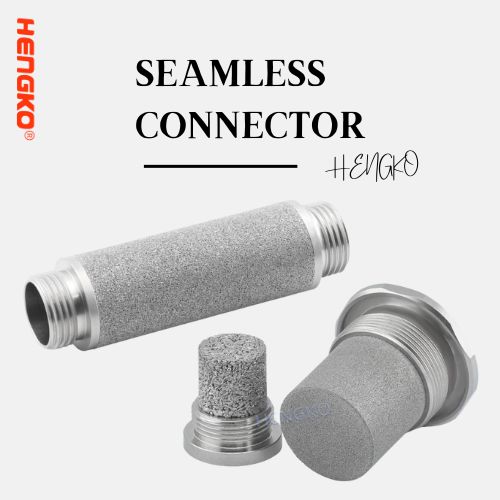
OEM seamless connector sintered metal cartridge
* OEM Sintered Cartridge By Application
Sintered metal cartridges are gaining traction in a variety of industrial filtration systems due to their superior physical attributes, including resistance to corrosion, acids, and alkalis, along with a firm and stable structure. Our cartridges can also be customized to various sizes and pore sizes based on your specific needs. So, whatever your application or project may be, contact HENGKO today to customize your unique sintered cartridge!
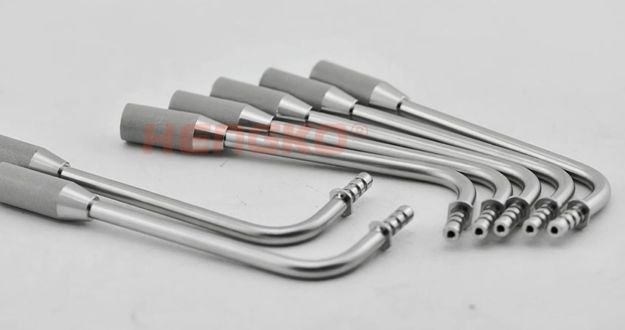
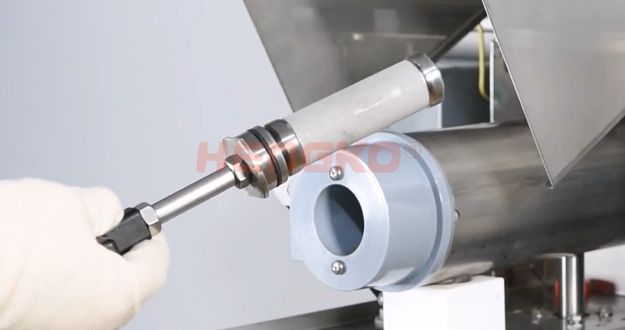
* Why Choose HENGKO OEM Your Special Sintered Cartridge Filter
HENGKO is a highly experienced manufacturer of stainless steel sintered cartridge. With years of experience in the sintered metal filter field, we have established a reputation for producing high-quality and reliable filter cup that are widely used in various industries over 50 countries.
1. High-Quality Materials:
Our sintered filter cartridge are made using advanced technology and high-quality materials, like 316L stainless ensuring that they are durable, long-lasting, and efficient in their filtration performance. HENGKO uses a unique sintering process that produces porous cartridge filter with high porosity and uniform distribution of pores, resulting in a highly efficient filtration process.
2. OEM Service;
HENGKO's sintered filter cartridge offer rich OEM service, in various sizes, shapes, and materials to meet the diverse needs of their customers. They are suitable for use in a wide range of applications, including gas and liquid filtration, air purification, water treatment, and many more.
3. Expert After Service:
For high-quality 316L SS Cartridge, HENGKO also provides excellent customer service, including technical support and after-sales service, ensuring that their customers are satisfied with their products and services.
Overall, HENGKO is a reliable and trustworthy manufacturer of sintered filters, and our commitment to quality and customer satisfaction makes HENGKO to be a top choice for businesses and industries in need of high-quality filtration solutions.
* Who We Worked With us
With years of design, development and production of sintered filters, HENGKO has maintained long-term close cooperation with many world-class universities and research laboratories in various fields. If you also need customized any special sintered filters, please get in touch with us immediately. HENGKO will provide the best filtering solution that solves all of your filtering problems.

* What You Should Do to OEM Sintered Cartridge filter - OEM Process
Once you've finalized your concept for a customized sintered cartridge, feel free to reach out to our sales team to discuss the details of your design and technical data requirements. We can then proceed with creating a sample of your bespoke sintered cartridge filter. For more information on the OEM process, please refer to the following details. We hope this facilitates a smooth collaboration. Share your vision with us today!
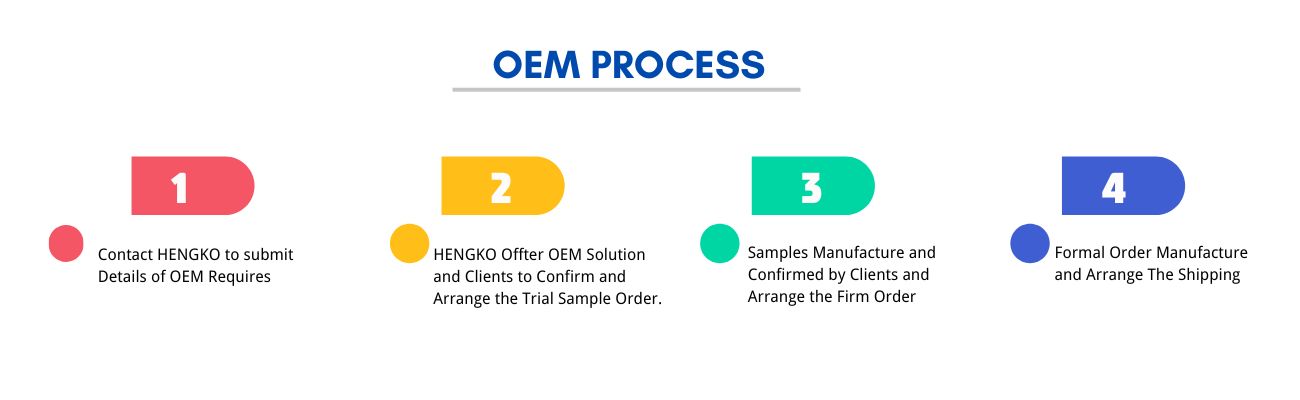
* FAQ about Sinered Cartridge ?
As Follow are some FAQ about sintered disc clients often asked, hope those will be helpful.
A sintered metal cartridge is a type of filter cartridge element, It is made of metal powder that is compacted and sintered to create a porous material that can filter fluids and gases. Till Now we main use the 316L stainless steel because the Excellent performance and low cost than others. Also the porous structure allows the fluid or gas to flow through the filter, while trapping contaminants or particles. So you can get the Purer Gases and Liquids.
Actually, Sintered metal cartridges are mainly used for filtration of fluids and gases in various industries such as chemical, pharmaceutical, food and beverage, and water treatment. They are usually used to remove impurities, particles, and contaminants from the fluids or gases. Because we can OEM different pore size to intercept smaller Impurities.
Sintered metal cartridges are commonly made from 316L, 316, Bronze, Inco Nickel, and various Composite Materials, among others. Which material to use depends on the application and the fluid or gas being filtered. So if you need to confirm which materials to use for your filtration elements, please contact us and tell us your condition to use the sintered cartridges.
Sintered metal cartridges provide excellent physical properties, such as resistance to corrosion, acids, and alkalis. They also have a firm and stable structure and can be customized to specific sizes and pore sizes based on your needs.
Selecting the correct pore size for your sintered cartridge is crucial to achieving the desired level of filtration efficiency while maintaining an appropriate flow rate. The pore size determines what size particles can be effectively filtered out while allowing the desired fluid to pass through. Here are the steps to help you select the right pore size for your sintered cartridge:
-
Understand Your Application: Start by understanding the nature of the fluid you're filtering and the particles or contaminants you want to remove. Consider factors such as particle size distribution, particle type (e.g., solids, liquids), and any potential variations in particle sizes.
-
Identify Filtration Goals: Determine your filtration goals. Are you aiming for coarse filtration to remove larger particles, fine filtration for smaller particles, or submicron filtration for extremely small contaminants?
-
Particle Size Analysis: Conduct a particle size analysis of the fluid to be filtered. This will provide valuable information about the range of particle sizes present. This data will help you determine the minimum pore size required to capture the particles of concern.
-
Select Pore Size Range: Based on the particle size analysis, identify a pore size range that can effectively capture the desired particles. The pore size should be smaller than the smallest particles you want to remove but large enough to avoid excessive pressure drop.
-
Consider Flow Rate: Keep in mind that smaller pore sizes can result in greater pressure drop and reduced flow rates. Balancing filtration efficiency with acceptable flow rates is important for efficient system operation.
-
Consult Manufacturer Data: Sintered metal cartridge manufacturers often provide data sheets that list the particle size retention capabilities of their cartridges. These specifications can help you match your filtration needs with the appropriate pore size options.
-
Trial and Testing: If possible, conduct tests using sintered cartridges with different pore sizes to determine which one performs best for your specific application. Evaluate factors such as filtration efficiency, flow rate, pressure drop, and cartridge lifespan.
-
Consider Particle Loading: Consider how much particle loading the cartridge will experience before needing replacement. A cartridge with larger pores might have a longer lifespan in applications with higher particle concentrations.
-
Future Changes: Anticipate any potential changes in your process that could affect particle size or loading. Choose a pore size that can accommodate these changes without frequent cartridge replacement.
-
Consult Experts: If you're unsure about the appropriate pore size, consult with filtration experts or the manufacturer's technical support team. They can provide valuable insights based on their experience and knowledge.
Remember that the pore size selection is a critical aspect of effective filtration. It's essential to strike a balance between filtration efficiency, flow rate, and pressure drop to ensure the sintered cartridge performs optimally for your specific application.
Yes, sintered metal cartridges can indeed be customized to meet specific requirements and applications. Sintering is a manufacturing process that involves compacting and heating metal powder until it fuses together, creating a solid piece. Sintered metal cartridges are commonly used in filtration applications where they offer excellent filtration efficiency and durability. The customization of these cartridges can involve various aspects:
-
Material Selection: The choice of metal powder for sintering can be tailored based on factors such as the type of fluids being filtered, temperature, and chemical compatibility.
-
Pore Size and Structure: The size and distribution of pores within the sintered metal can be adjusted to achieve the desired filtration efficiency and flow rate.
-
Cartridge Dimensions: Custom cartridges can be designed to fit specific filter housings or systems. This includes variations in diameter, length, and overall shape.
-
End Caps and Fittings: The end caps of the cartridge, as well as the inlet and outlet fittings, can be customized to match the connection requirements of the filtration system.
-
Surface Treatment: Custom surface treatments can be applied to enhance features such as corrosion resistance, ease of cleaning, or to modify the surface for compatibility with certain fluids.
-
Support Structures: For more complex applications, sintered cartridges can be designed with support structures to withstand higher pressures or to maintain structural integrity in demanding conditions.
-
Multi-Layered Cartridges: Some applications may require multiple layers of different sintered metals or mesh sizes to achieve specific filtration goals.
-
Special Coatings: Additional coatings or treatments can be applied to the sintered cartridge to improve its performance in extreme conditions or for specialized applications.
-
Certifications and Compliance: Customized cartridges can be designed to meet specific industry standards and regulations, ensuring they are suitable for use in particular industries.
-
Flow Characteristics: The geometry of the cartridge can be customized to optimize flow distribution and minimize pressure drop across the filter media.
When considering customization of sintered metal cartridges, it's important to collaborate with manufacturers or experts experienced in sintering technology. They can provide guidance on material selection, design considerations, and feasibility based on the intended application. Customization offers the advantage of tailoring the filtration solution to the unique needs of a given process or industry.
The lifespan of a sintered metal cartridge depends on several factors, including the operating environment, usage frequency, and maintenance. Regular cleaning and appropriate usage can significantly extend its lifespan.
Cleaning a sintered metal cartridge is essential to maintain its filtration efficiency and prolong its lifespan. The cleaning process depends on the type of contaminants being removed and the nature of the filtration system. Here's a general guide on how to clean a sintered metal cartridge:
Materials Needed:
- Water or appropriate cleaning solution
- Soft brush or sponge
- Compressed air (if available)
- Safety gloves and goggles (if using cleaning chemicals)
Steps:
-
Preparation: Ensure that the filtration system is turned off, and any pressure or fluid flow is relieved before you start the cleaning process.
-
Removal from System: Remove the sintered metal cartridge from the filtration system following the manufacturer's guidelines.
-
Initial Inspection: Inspect the cartridge for visible signs of clogging, fouling, or buildup. This will help you determine the extent of cleaning needed.
-
Rinsing: If the cartridge is lightly soiled, you may be able to rinse it with water. Gently spray water through the cartridge in the reverse direction of the normal flow to dislodge and remove loose contaminants.
-
Chemical Cleaning (if required): For more stubborn contaminants, you might need to use a mild cleaning solution. Follow these steps if using a cleaning solution:
a. Mix the appropriate cleaning solution as recommended by the manufacturer or an expert. b. Immerse the cartridge in the solution for a specific period (usually recommended by the manufacturer). Avoid using aggressive chemicals that could damage the cartridge. c. Gently agitate the cartridge in the solution to help dislodge and dissolve contaminants.
-
Mechanical Cleaning: Use a soft brush, sponge, or soft cloth to gently scrub the external surface of the cartridge. Be cautious not to damage the sintered metal surface. Avoid using abrasive materials or brushes that could cause scratching.
-
Backflushing: Backflushing involves directing water or cleaning solution through the cartridge in the opposite direction of the normal flow. This can help dislodge and remove contaminants that are trapped within the pores. Use low-pressure water or air for this process.
-
Rinsing and Drying: Thoroughly rinse the cartridge with clean water to remove any traces of cleaning solution or loosened contaminants. Allow the cartridge to air dry completely before reinstallation. Compressed air can be used to help accelerate drying.
-
Inspection and Reinstallation: Inspect the cleaned cartridge for any remaining contamination or damage. If it appears clean and intact, reassemble the filtration system and reinstall the cartridge.
-
Regular Maintenance: Implement a regular maintenance schedule based on the operational conditions of your system. Cleaning intervals will vary based on factors such as the nature of contaminants, flow rates, and the environment.
Always follow the manufacturer's guidelines for cleaning and maintenance to avoid any damage to the sintered metal cartridge. If you're unsure about the cleaning process, consider consulting the manufacturer or a filtration expert for guidance tailored to your specific cartridge and application.
Installation instructions may vary depending on the specific filtration system. Detailed installation guidelines are typically provided with the product or available from the manufacturer's customer support.
HENGKO's team is committed to providing comprehensive support for our customers. If you have questions or need assistance, our customer service and technical teams are ready to help.
* You May Also Like
HENGKO offers a wide variety of sintered filters suitable for various applications. Please find a list of our available sintered filters below. If any of these pique your interest, feel free to click on the corresponding link for more information. To receive pricing details today, reach out to us at ka@hengko.com.